Exploring 3D Printing: Principles and Applications
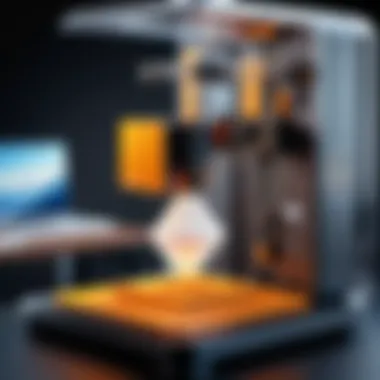
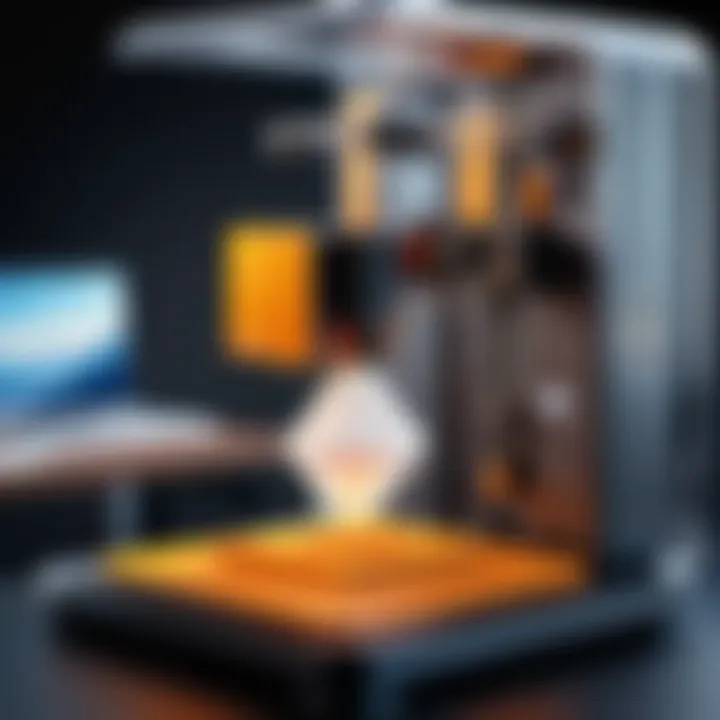
Intro
3D printing, often dubbed additive manufacturing, epitomizes a technological renaissance that has transcended the boundaries of traditional manufacturing. This technology has morphed from a niche within prototyping to a mainstay in industries as diverse as aerospace, healthcare, and even fashion. The overarching narrative of this article delves into the core principles of 3D printing and its myriad applications, dissecting how this technology reshapes the frameworks of design and production. What makes it fascinating is not merely the capability to create objects layer by layer but the potential to revolutionize production processes and embrace sustainability, all while enabling extraordinary design flexibility.
To fully understand its influence, it's crucial to explore both its historical evolution and cutting-edge technologies that drive it forward.
In the unfolding sections, we will touch upon:
- The foundational elements that make 3D printing stand out.
- Technical specifications and their relevance to applications.
- Design aesthetics and durability considerations in material choice.
- The impact on various sectors, from IT to manufacturing.
Overview of Product Features
3D printing technologies are varied, yet they share a common goal: to construct physical objects from digital designs. Several notable features characterize these technologies. They range from the types of materials employed to the specific methods of layer application, underscoring a broad spectrum of capabilities.
Key Specifications
Different 3D printing techniques present unique specifications that contribute to their efficacy in specific applications. Some noteworthy specifications include:
- Layer Resolution: Crucial for the final object's detail level. Higher resolutions yield finer details but often increase production time.
- Build Volume: Defines the maximum size of the object that can be manufactured; larger volumes allow for more significant parts but come with additional complexity.
- Material Compatibility: Not all printers work with every material. Understanding the right combination is essential for successful outcomes.
Unique Technologies
In the sphere of 3D printing, various technologies stand out due to their unique approaches and advantages:
- Stereolithography (SLA): Uses UV light to harden resin models layer by layer.
- Fused Deposition Modeling (FDM): Extrudes melted plastic filament to produce objects. This is popular for its affordability and accessibility.
- Selective Laser Sintering (SLS): Utilizes a laser to fuse powdered materials, providing robust structures.
Each of these technologies is tailored to specific needs, and understanding these nuances is pivotal for IT professionals conceptualizing applications in their respective fields.
"3D printing not only streamlines production but creates a dialogue between the digital and physical worlds, leading to innovative solutions."
Design and Build Quality
When discussing the production of 3D printed objects, both the design and build quality play critical roles in determining the success of the final product. The attributes that comprise design and build quality extend beyond mere aesthetics. They encapsulate functionality and practical application as well.
Aesthetics
A crucial component for any object, aesthetic appeal becomes particularly important in sectors like fashion and consumer products. High-quality finishes, vibrant colors, and innovative designs can make the difference between market success and mediocrity. Graphic designers often exploit the design flexibility offered by 3D printing, allowing for intricate shapes and structures that traditional methods could not achieve.
Material Durability
Material choice affects not only aesthetics but also the longevity and endurance of the final product. For example, polycarbonate materials are preferred for functional components due to their robustness, while simpler plastics might suffice for prototype models.
The decision on materials needs to align with the intended use, balancing factors like cost, resilience, and visual appeal.
Foreword to 3D Printing
In the current manufacturing landscape, the significance of 3D printing cannot be overstated. Known for its transformative potential, 3D printing, also known as additive manufacturing, opens doors to innovative approaches across a plethora of fields. In this section, we will dive into its historical context and define what 3D printing truly encompasses.
Historical Context
Tracing back to its origins, 3D printing began as a concept in the early 1980s, primarily spearheaded by Charles Hull, who developed the first stereolithography device in 1983. This marked a pivotal moment when technology transitioned from traditional subtractive methods to additive ones, leading to the gradual evolution of printing techniques. Over the next decades, advancements came swiftly. In the 1990s, the technology matured, emerging into various processes like fused deposition modeling and selective laser sintering.
By the 2000s, patents began to expire, allowing for a boom of innovation and accessibility. It’s fascinating to note how the arrival of the Maker movement in the 2010s sparked interest among enthusiasts and hobbyists. Suddenly, 3D printing wasn't reserved for industrial giants; it found a home in garages and classrooms. This democratization of technology paved the way for a new generation of makers and inventors, signifying a shift in how products are designed and manufactured. It's like having a factory at your fingertips!
Define 3D Printing
So, what is 3D printing? At its core, 3D printing is a process of creating three-dimensional objects from a digital file. The magic lies in additive techniques where layers of material are stacked to form a final product. Unlike traditional manufacturing where material is carved away, 3D printing builds an object layer by layer, which can lead to remarkable savings in both material waste and time.
Typically, this process begins with a 3D model, usually designed using CAD software or acquired through 3D scanning. Materials utilized can vary widely—from plastics, metals, to even biological substances for bioprinting applications in healthcare. The versatility is what sets it apart, enabling the creation of complex geometries and designs that were once considered impossible to fabricate. It’s akin to having an artist’s canvas where every detail can be sculpted with precision.
"3D printing is not merely a manufacturing method; it represents a new paradigm in how we think about production, customization, and efficiency."
Key Technologies in 3D Printing
The significance of Key Technologies in 3D Printing cannot be overstated. These technologies serve as the backbone of the entire 3D printing ecosystem. By understanding these processes and methods, we can better appreciate how 3D printing transforms both traditional manufacturing norms and modern innovation strategies. Each technology has its own unique advantages and applications, giving rise to a diverse range of possibilities in product development, design creativity, and even sustainability practices.
Additive Manufacturing Processes
Additive manufacturing, often referred to simply as 3D printing, involves creating objects by layering materials based on digital models. This contrasts sharply with subtractive manufacturing methods that cut away material from a solid block. The benefit of additive techniques lies in their capacity to reduce waste and enable complex geometries that traditional methods struggle to produce.
For instance, consider how aerospace parts are crafted. Engines designed using additive manufacturing can feature intricate cooling channels that improve performance, reducing weight while enhancing efficiency. This technology invites innovation without the confines of conventional manufacturing limitations, which can yield enormous cost savings in both materials and production time.
Material Extrusion Techniques
Material extrusion is perhaps the most recognized process in 3D printing. It’s best exemplified by Fused Deposition Modeling (FDM), widely used in home 3D printers. This method feeds thermoplastic filament into a heated nozzle, which melts the plastic and extrudes it layer by layer. The ease of use and relative affordability of material extrusion makes it appealing not just for hobbyists but also for start-ups looking to develop prototypes quickly.
The key consideration with extrusion techniques is material quality and temperature control. Varied materials, such as ABS, PLA, or nylon, offer diverse characteristics—each suitable for specific applications. For example, while PLA is biodegradable, it may not hold up against high temperatures compared to ABS. This necessitates a careful selection of materials based on intended usage.
Stereolithography and its Variants
Stereolithography (SLA) was one of the earliest 3D printing technologies developed and remains relevant today. It works by utilizing ultraviolet light to cure photopolymer resin layer by layer. This method excels in producing exceptionally detailed and smooth surfaces, making it ideal for applications requiring high precision, like dental models or intricate jewelry designs.
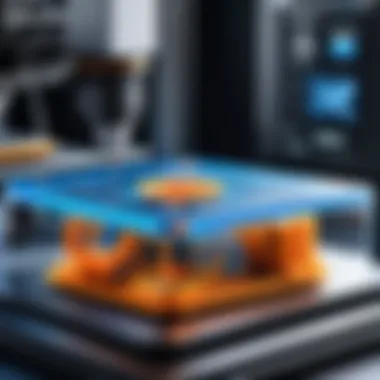
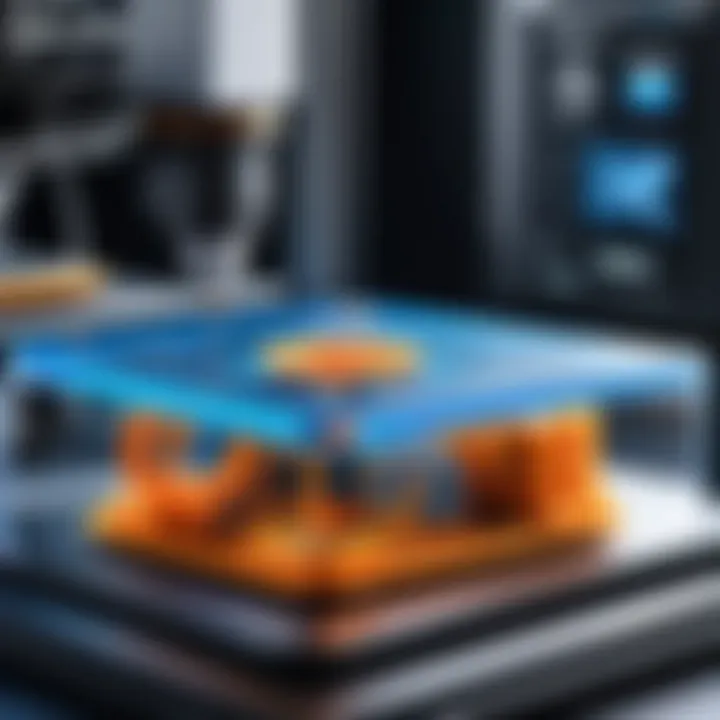
However, with precision comes a challenge: the materials often require post-processing, such as washing and curing. Innovations have led to variants like Digital Light Processing (DLP), which employs a digital projector to cure entire layers simultaneously, speeding up the process considerably. Each variant presents different efficiency levels and resolution capabilities, thus influencing the decision-making process for creators based on their specific needs.
Powder Bed Fusion Methods
Powder Bed Fusion encompasses techniques such as Selective Laser Sintering (SLS) and Electron Beam Melting (EBM). These methods use lasers or electron beams to fuse powdered materials—often metals or polymers—into a solid structure. The advantages of Powder Bed Fusion are significant. Not only does it enable the production of highly complex parts, but it also allows for the use of materials that can’t be processed through traditional methods.
One of the striking benefits of SLS, for example, is its ability to create strong parts without the need for support structures, thanks to the surrounding powder. This makes it particularly valuable in industries such as automotive and aerospace, where lightweight and robust components are critical. Yet, the machinery and operational costs can be a barrier to entry, often relegating this technology to larger manufacturing firms and specialized applications.
Key Takeaway: The evolution of these 3D printing technologies highlights the paradigm shift from conventional manufacturing to innovative, efficient approaches that prioritize creativity and sustainability. As industries embrace these advances, the perception of what’s possible in product design continues to expand.
Applications Across Industries
The versatility of 3D printing reaches across numerous industries, making its applications vital to the advancement in various sectors. From healthcare to aerospace, this innovative technology has fundamentally transformed practices and processes. Worth mentioning is how it fosters creativity while simultaneously addressing efficiency and customization. The ability to produce components on-demand revolutionizes supply chains and enables businesses to respond to market demands swiftly. Each industry leverages 3D printing in its unique way, which often leads to substantial reductions in material waste and production costs. Here's a deeper look into several sectors.
Healthcare Innovations
Prosthetics and Orthopedics
When discussing prothesis and orthopedics, it's hard not to admire how 3D printing reshapes the landscape. The key characteristic here is personalization. Each prosthetic limb can be custom-fitted to match the individual's anatomy. This tailored approach enhances comfort and usability for patients. The unique capability to scan and print a precise replica of a patient’s limb reduces the time from design to production, offering new hope to many.
Advantages of this technology include:
- Cost Reduction: Traditional manufacturing can be labor-intensive and expensive, while 3D printing often requires fewer materials and less labor.
- Rapid Production: Speed is essential in healthcare; the ability to quickly deliver custom prosthetics means patients can return to their daily lives more swiftly.
While it's remarkable, it’s not without its challenges, such as regulatory scrutiny and the materials used being less durable than traditional methods.
Bioprinting of Tissues
Bioprinting represents a significant leap in medical science. This innovative method allows for the printing of tissues that can replicate both the structure and function of human organs. Its key characteristic is the incorporation of living cells into a 3D structure. This opens up avenues that could lead to organ transplants without rejection issues. Bioprinting is particularly beneficial in research settings, where tissue samples from patients can be created for testing drugs.
Some unique features include:
- Customization: Tissues can be designed to match patient-specific requirements.
- Decreased Wait Times: With a potential decrease in the need for donors, patients could receive essential treatments quicker.
However, ethical barriers and complexity of replicating vascular systems stand as significant hurdles.
Automotive Advancements
Rapid Prototyping
The realm of automotive advancements undoubtedly benefits from rapid prototyping. This process allows engineers to quickly create a physical model of a design, facilitating a hands-on examination. The primary advantage lies in its speed; engineers can iterate designs in a fraction of the time it would normally take.
Key benefits of rapid prototyping include:
- Enhanced Collaboration: Teams can visualize ideas, leading to better teamwork.
- Cost Savings: Rapid prototypes can dramatically cut costs associated with traditional modeling techniques.
Amongst its drawbacks, the accuracy of rapid prototypes and limitations on material types can sometimes lead to discrepancies with final products.
Customization of Parts
When it comes to customization of parts, 3D printing shines by allowing manufacturers to create tailored components for vehicles. From personalized dashboard features to unique mirror designs, this flexibility means that customers can have a real say in their vehicles.
Characteristics of this customization include:
- Consumer Engagement: Customized components can enhance a buyer’s connection with their vehicle.
- Diminished Inventory Needs: Manufacturers can print parts as needed instead of maintaining bulky inventories.
Yet, issues like durability and balance between customization and production speed must be taken into account.
Aerospace Manufacturing
Lightweight Components
Aerospace has embraced lightweight components created by 3D printing, which result in more fuel-efficient aircraft. They do this by using less material without compromising strength, a real game-changer in aviation design. The unique material combinations lead to designs that are not just lighter but also more robust, addressing both performance and fuel economy.
Advantages include:
- Fuel Savings: Less weight translates to lower fuel consumption.
- Extended Range: Lighter planes increase travel distance.
However, concerns about the longevity of 3D printed materials under extreme conditions remain a topic of ongoing research.
Complex Geometries
With complex geometries, 3D printing allows engineers to design parts that traditional methods could never achieve. This is especially useful in the aerospace sector, where streamlined shapes can drastically enhance performance.
Its defining trait is the ability to produce intricate designs that significantly reduce part count.
Benefits such as:
- Efficiency in Manufacturing: Fewer components mean simpler assembly.
- Innovative Design Flexibility: Engineers can push the limits of design without the constraints of traditional manufacturing practices.
Though, achieving the perfect design still requires comprehensive testing to ensure safety.
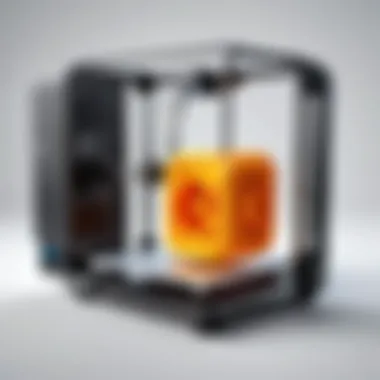
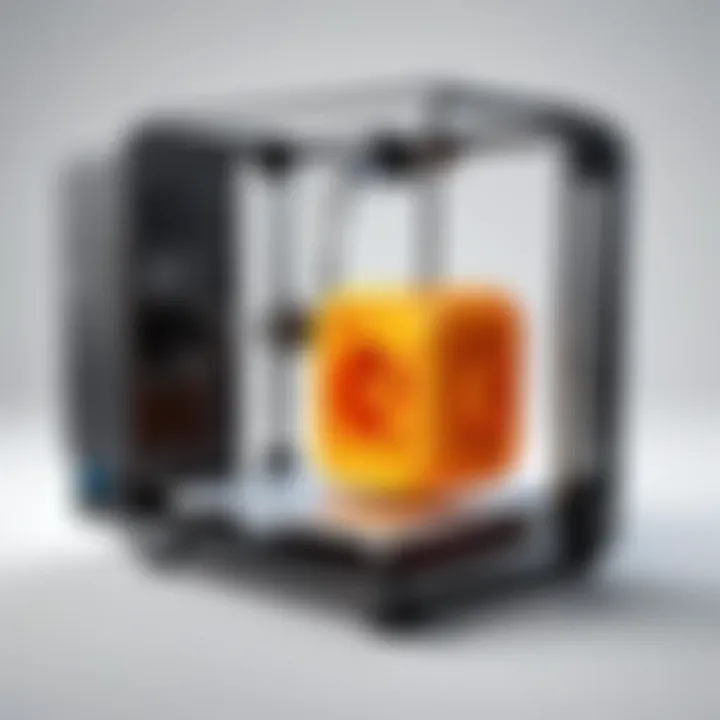
Consumer Goods and Fashion
Tailored Products
The consumer goods market has been revolutionized by the capability to produce tailored products. With the onus on customization, brands offer bespoke items that cater specifically to individual tastes and preferences. This level of personalization not only enhances customer satisfaction but also boosts brand loyalty.
Noteworthy benefits of this approach are:
- Unique Value Proposition: Products are not readily available elsewhere, making them exclusive.
- Enhanced Interaction: Customers feel more connected to brands offering customized solutions.
However, balancing mass production with custom requests can pose its unique challenges.
Jewelry Design
In the world of jewelry design, artisans leverage 3D printing to create intricate and unique pieces that push the envelope of creativity. The standout feature here is the ability to translate imaginative designs directly into 3D models with remarkable efficiency, without compromising on artistic integrity.
Key attributes include:
- Complexity in Crafting: Jewelers can design and produce pieces that would be labor-intensive manually.
- Cost Effectiveness: Lesser material waste and quicker production times lead to financial savings.
Still, ensuring that the material used meets consumer expectations for quality and durability is critical.
Overall, the application of 3D printing across industries demonstrates its capacity to drive innovation. As each sector incorporates this technology, it shapes not just how products are designed and manufactured, but also how end-users engage with these products, ultimately leading to more streamlined and responsive production methods.
Advantages of 3D Printing
The advantages of 3D printing are significant and wide-reaching, making it an essential consideration for industries looking to innovate. As technology evolves, understanding these benefits helps organizations leverage 3D printing to enhance their operations. This section will delve into three major advantages, namely cost efficiency, rapid prototyping capabilities, and sustainability with waste reduction in focus.
Cost Efficiency
Cost efficiency stands out as one of the most compelling reasons companies adopt 3D printing techniques. Traditional manufacturing often involves high production costs due to extensive tooling and setup times. 3D printing, in stark contrast, can substantially trim these expenses.
- Reduction in Material Costs: With additive manufacturing, material is used only as needed, thus minimizing waste. Unlike subtractive methods, which cut away material from a solid block, printing layers only as required cuts down on excess.
- Lower Labor Costs: The automation of the 3D printing process means that fewer workers are needed for manufacturing tasks, enabling companies to reallocate personnel to more strategic roles. This also reduces the costs associated with hiring and training.
- Less Inventory: By producing parts on demand, businesses can significantly lower their inventory costs. There's no need to overproduce or store vast quantities of pre-made parts, which often ties up capital.
"In a world where every penny counts, 3D printing technology offers a breath of fresh air for businesses targeting leaner operations."
Rapid Prototyping Capabilities
Another standout advantage of 3D printing is its rapid prototyping capabilities. The ability to flow seamlessly from design to prototype in mere days, or even hours, provides significant competitive edge. Here are some key aspects:
- Quick Turnaround Time: Designers can produce prototypes far quicker than traditional methods allow. This acceleration in the development cycle means larger volumes can be generated, increasing the opportunity for testing and iteration.
- Design Flexibility: With 3D printing, designers can explore complex shapes and structures that would be impractical with conventional manufacturing. This flexibility can lead to innovative designs that enhance the performance or aesthetic appeal of a product.
- Testing and Feedback Loops: Rapid prototyping allows companies to test concepts directly in the hands of the consumer swiftly. Feedback loops can be established quickly, leading to a more attuned product that meets real user needs.
Sustainability and Waste Reduction
Sustainability is more than just a buzzword; it’s a pressing need for our modern age. 3D printing aligns well with environmental concerns, offering distinct advantages in sustainability:
- Material Efficiency: As mentioned earlier, 3D printing builds items layer by layer. This unique approach means there is minimal waste. A more efficient use of materials translates directly to a reduced carbon footprint.
- Localized Production: The ability to print items on-demand and close to the point of sale greatly reduces the need for extensive logistics. This not only slashes transportation emissions but also supports local economies.
- Recyclable Materials: Many 3D printers can utilize biodegradable or recyclable filaments. As technology progresses, using sustainable materials becomes easier, helping fight against the larger issue of plastic waste.
The advantages of 3D printing paint a compelling picture for companies aiming to stay ahead in an increasingly competitive landscape. From cost savings to environmental benefits, 3D printing isn't just a trend; it's a movement towards smarter and more efficient production.
Challenges in 3D Printing
When we talk 3D printing, we often get lost in the excitement of its capabilities and diverse applications. However, it’s crucial to also navigate the rough waters that this technology presents. Understanding the challenges in 3D printing is vital for anyone involved in the industry—not just for troubleshooting but also for pushing the boundaries of what’s possible. Each challenge can influence the effectiveness, reliability, and scalability of this technology.
Material Limitations
Materials used in 3D printing are central to the quality and functionality of the printed objects. Different techniques require specific materials, and not all materials are created equal. For example, while plastic and resin might be used widely, complex materials that could inspire new innovations are still in nascent stages.
Here are a few key points to consider:
- Strength and Durability: Some materials lack the strength required for high-stress applications. Using low-quality materials can lead to failures; thus, even best printers cannot save the project.
- Cost of Advanced Materials: Materials like titanium or carbon fiber offer great benefits but come with a hefty price tag. That might stifle smaller companies from exploring these advanced options.
- Range of Material Types: The scope of materials is still very limited compared to traditional manufacturing. While some advancement is happening, industries are yearning for a broader selection.
A blockquote that defines the material challenges can shine a light here:
"While 3D printing offers a universe of possibilities, it's often the type of materials that can pull the rug from under your best laid plans."
Quality Control Issues
Quality control stands as a significant hurdle in 3D printing. Unlike traditional manufacturing, where processes are standardized, 3D printing often depends on the finesse of the operator and the specifics of the materials used. This variability leads to inconsistency in the final products.
Important considerations include:
- Process Variability: Parameters such as temperature or speed need constant monitoring. Small deviations can result in defects that are sometimes invisible to the naked eye.
- Post-Processing Needs: Many 3D printed items require post-processing, which can further add to the chances of defects emerging. This might involve sanding, painting, or other methods which introduce risks.
- Surface Finish and Tolerance: Products often require tighter tolerances than what 3D printing can reliably achieve, especially when it comes to functional parts.
Quality control issues require continuous refinement, calling for regular updates on machinery and training personnel to maintain standards.
Regulatory Hurdles
Regulation always lags behind innovation, and 3D printing is no exception. Industries demand oversight to ensure safety and efficacy, particularly in sectors like healthcare and aerospace. However, crafting regulations that are flexible enough to keep pace with this fast-evolving technology remains challenging.
Key points of concern include:


- Lack of Standardization: Different countries approach regulations in varying manners. This adds complexity for companies who operate globally, complicating compliance.
- Intellectual Property Challenges: The ease of copying designs can lead to a legal minefield regarding patents, inhibiting innovation as companies tread carefully around ownership.
- Safety and Liability Issues: With consumer-grade 3D printers becoming ubiquitous, regulatory bodies are scratching their heads over liability. If a product fails, who bears responsibility—the manufacturer of the printer, the material supplier, or the designer?
Overcoming these regulatory challenges is essential for broader acceptance of 3D printing across industries, ensuring safety while not stifling creativity.
3D Printing in Information Technology
In the sprawling landscape of technological innovations, 3D printing stands out not only for its creative potentials but also for its profound integration in the realm of information technology. The marriage of 3D printing and IT has birthed a new era in manufacturing, design, and even service delivery. Emphasizing flexibility and efficiency, its applications extend to software development, data management, and infrastructure optimization, making it an essential ingredient in the recipe of modern technology.
Technology is always evolving, but 3D printing provides tools for that evolution. Take for instance, the resources needed to prototype new items; this might usually involve hours of labor and a multitude of materials. However, with 3D printing, many of these tasks can be simplified by software that directly interfaces with the printers. Integrated software can lead to improvements in how products are developed and how information is shared.
"The incorporation of 3D printing into IT proves that when software meets hardware innovation, magic happens."
Integration with Software Development
The synergy between 3D printing and software development showcases how advancing technology can ripple through industries. Think of software developers as the architects of digital tools that make the physical applications of 3D printing more accessible. They create platforms that allow designers to model their ideas and translate them into prints with relative ease.
However, it doesn't stop there. There are multiple stages in product lifecycle management where software facilitates smoother transitions from concept to reality. For example,
- CAD software, like SolidWorks or AutoCAD, enables designers to create detailed models that 3D printers can interpret.
- Slicing software converts those 3D models into a series of two-dimensional layers that the printer can understand, ensuring accuracy in production.
- Simulation software provides the ability to evaluate a prototype's performance before a single layer of material is laid down.
As we lean toward cloud solutions, collaborative platforms are growing. Teams can work on projects from different corners of the world using tools that share updates in real-time. This interconnectedness not only promotes creativity but also makes the overall design process adaptable to changes.
Impact on IT Infrastructure
The ripple effect of 3D printing on IT infrastructure cannot be underestimated. Systems that were built for traditional manufacturing practices are now transforming to accommodate the demands of additive manufacturing. Companies investing in 3D printing need to reassess their IT infrastructure to ensure it meets high-speed and capacity requirements.
This involves rethinking data storage, computing power, and network capabilities since large CAD files and printer configurations consume significant bandwidth. Think of it this way: a company that used to consult a few suppliers for a product now might possess the ability to modify designs on-demand and print them locally. This shift requires nimble IT ecosystems that can manage these vast changes seamlessly.
The advent of 3D printing also enforces a need for robust cybersecurity measures to protect sensitive design information. Business integrity relies on safeguarding intellectual property, and as printers become increasingly networked, the risk of data breaches rises. Companies must be equipped with firewalls, encryption, and regular system audits to steer clear of potential pitfalls.
In summary, the convergence of 3D printing and information technology is not just a novelty; it reshapes the very foundation of how products are created, shared, and manufactured. With its unique offerings, 3D printing promises to revolutionize the interactions between technology and industries, paving the way for future innovations.
In this fast-paced world, being ahead is paramount, and understanding the nuances of 3D printing in IT is a step toward not only keeping pace but also leading the charge toward a more digitized tomorrow.
Future Prospects of 3D Printing
As we look ahead, the realm of 3D printing technology appears to be on the cusp of a transformative boom. Its potential extends far beyond mere novelty, inviting explorations into new realms of efficiency and creativity, while also disrupting traditional production methodologies. In this segment, we shall unpack the various dimensions that signify the future paths of this fascinating technology, paying particular attention to emerging technologies, market growth, and its symbiotic role in Industry 4.0.
Emerging Technologies
The tides of innovation continue to favor 3D printing, introducing a suite of emerging technologies that enrich its landscape. One of these is Continuous Liquid Interface Production (CLIP), a process developed by companies like Carbon that enables faster printing through a unique curing method. By utilizing ultraviolet light to solidify resin, CLIP can produce parts in a matter of minutes—an extraordinary leap from traditional methods.
Another notable advancement is Multi-material 3D printing. This technology allows for the creation of objects composed of different materials within a single print job. This not only offers enhanced functionality but also lets designers play more freely with aesthetics.
- Digital Light Processing (DLP), like SL, casts light onto resin but processes layers faster, offering practicality for larger projects.
- Binder Jetting uses liquid binders to bond powdered materials, streamlining production while minimizing waste.
As these technologies continue to mature, they promise to blur the lines between prototyping and full-scale production, carving a niche for 3D printing in commercial applications.
Potential Market Growth
The market for 3D printing is projected to expand at an incredible pace, driven by the relentless pursuit of efficiency and customization. Analysts forecast the global 3D printing market to reach nearly $70 billion by 2027. Several factors contribute to this projection:
- Increase in customization demand: Consumers increasingly seek personalized products, and 3D printing offers a unique avenue for tailor-made solutions.
- Cost-effective manufacturing: As the technology improves, the cost of 3D printers and materials will likely continue to decline, making this accessible to smaller businesses as well.
- Global supply chain optimization: Companies are exploring local production solutions to minimize delays and inefficiencies, and 3D printing serves as a powerful tool in this respect.
The potential for growth is not just limited to manufacturing but also spans across diverse sectors, including healthcare, automotive, and even fashion, as the appetite for innovative and efficient solutions persists.
Role in Industry 4.
Industry 4.0 marks a new epoch in manufacturing characterized by smart technology integration, and 3D printing occupies a significant position within this paradigm. It synergizes with core Industry 4.0 concepts, such as the Internet of Things (IoT), big data, and artificial intelligence.
- Data-driven production: 3D printers can be monitored and controlled through IoT, allowing for adjustments in real-time based on performance metrics.
- Customizable manufacturing: AI can inform design protocols for unique requirements, making the process smarter as more data becomes available.
- Efficient resource allocation: Analyzing data allows companies to optimize material usage, directly aligning with sustainability goals while cutting costs.
"When deployed smartly, 3D printing not only enhances production efficiency but also lays the groundwork for new business models, amplifying the collective intelligence of organizations in the digital age."
As we venture further into this decade, 3D printing’s role in Industry 4.0 will grow, presenting opportunities for IT professionals and businesses to rethink what is achievable in manufacturing.
In summation, the future prospects of 3D printing are robust and multifaceted, signaling a revolutionary journey ahead. As emerging technologies will reshape capabilities, coupled with significant market growth and its integration into Industry 4.0, the implications are monumental for various sectors.
The horizon gleams a bright promise, urging us to keep an eye on this space as it evolves.
The End
The unfolding narrative of 3D printing technology underscores its pivotal role in various sectors, shaping the future of manufacturing and design. In this article, we’ve traced its historical roots and technological milestones, and now we can appreciate the importance of synthesizing findings and recognizing lasting implications.
Summary of Findings
We’ve explored how 3D printing is not just a passing trend, but rather a game-changing method that reinvents traditional practices. Here are the key takeaways:
- Advancements in Applications: From healthcare's bespoke prosthetics to aerospace's lightweight components, every sector is experiencing a metamorphosis thanks to this technology.
- Efficiency and Sustainability: Businesses are finding themselves cutting costs and minimizing waste, affirming that practicality and environmental consciousness can coexist.
- Challenges Ahead: Despite the vast potential, the road is not without hurdles such as material limitations and regulatory frameworks that must evolve over time.
Lasting Implications
The implications of these advancements are profound and multifaceted. As we look ahead, consider the following points:
- Innovation in Design and Production: The ability to rapidly prototype and customize designs will lead to more unique products, potentially revolutionizing consumer expectations.
- Impact on Job Market: While some traditional manufacturing jobs may diminish, new roles focused on design and technology integration are likely to emerge, requiring a shift in workforce skills.
- Future of Industry: As 3D printing becomes ingrained in Industry 4.0, its integration with AI and IoT could lead to smarter manufacturing processes that are efficient and responsive to market needs.
"The advent of 3D printing will not only change how we make things but could fundamentally alter our approach to design and efficiency in myriad ways."