Choosing the Best 3D Printer for Miniatures
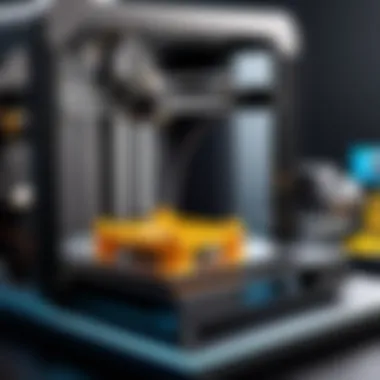
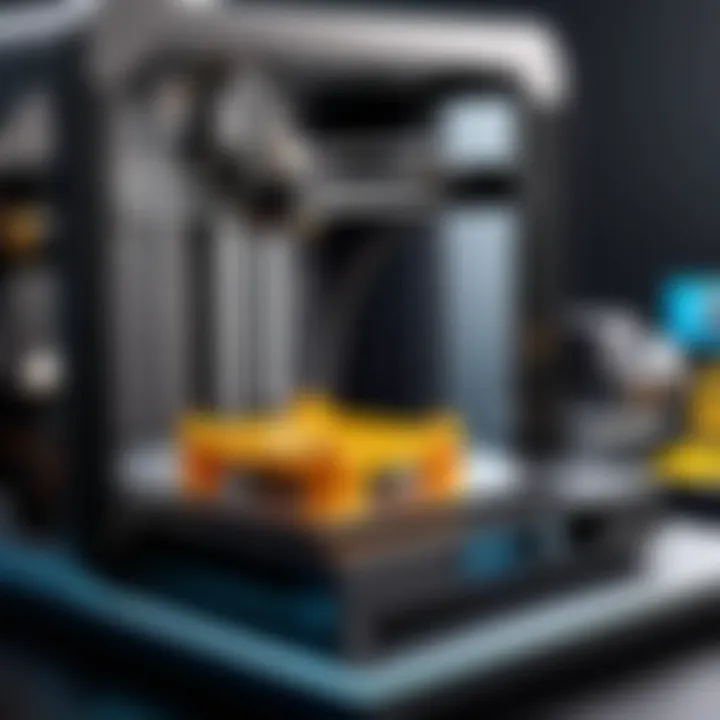
Intro
In recent years, the world of crafting has seen a revolution, largely due to the emergence of 3D printing technology. Particularly for hobbyists and professionals involved in miniature creation—from tabletop games to detailed architectural models—the right 3D printer can make all the difference. Selecting an ideal 3D printer is no small feat, given the plethora of options available today. Just like choosing the right tool for a job, making a well-informed decision requires careful consideration of several factors.
This article is set out to illuminate the pathway to selecting a 3D printer that not only meets but exceeds your expectations when it comes to producing high-quality miniatures. We will break down crucial criteria such as print resolution, speed, material compatibility, and the overall user experience.
Overview of Product Features
Choosing a 3D printer is largely about understanding its features. Let's dive deeper into some essential specifications that make a printer worth its salt.
Key Specifications
When it comes to 3D printers for miniatures, certain specifications hold paramount importance:
- Print Resolution: This refers to how finely a printer can render details. A higher resolution yields smoother surfaces and finer details, which is critical for intricate designs.
- Layer Height: Ideally, a layer height of 0.1mm or less is preferred for miniatures, allowing for more detail to be captured.
- Print Speed: While quality is crucial, speed also matters if you plan to produce multiple miniatures in a shorter time frame. However, there’s often a trade-off: faster printing can sometimes lead to compromised quality.
- Build Volume: Ensure the printer you choose can accommodate the size of your intended models. A larger build volume allows for greater flexibility in design.
Unique Technologies
Different printers employ various technologies to achieve printing:
- Fused Deposition Modeling (FDM): Often more budget-friendly, FDM printers work by extruding melted filament layer by layer. While they are versatile, they may not always deliver the sharpest details required for miniatures.
- Stereolithography (SLA): This method uses a laser to cure resin into solid, high-precision prints. SLA is favored for miniatures due to its ability to render minute details sharply.
- Digital Light Processing (DLP): Similar to SLA, DLP utilizes a light source to harden liquid resin, often resulting in quicker print times compared to SLA, without sacrificing quality.
Design and Build Quality
Ultimately, the design and build quality of the printer can also affect your experience using it. Not all printers are created equal, and some factors can lead to a more enjoyable printing journey.
Aesthetics
While functionality reigns supreme, an aesthetically pleasing machine certainly wouldn’t hurt. A printer that fits comfortably within a workspace, both in terms of size and design, will bring satisfaction to its user. Consider whether you’d prefer a sleek, modern design or something more traditional. Either way, the look can play a role in your choice.
Material Durability
A 3D printer's construction materials can make a difference in its lifespan and performance. Common materials include:
- Plastic: Generally lightweight but may wear down faster.
- Metal Components: Offer greater durability and withstand heavy usage. While often more expensive, they can justify the investment over time.
"Invest in quality at the outset, as a good printer will save you both time and money in the long run."
Prologue to 3D Printing for Miniatures
When discussing the world of hobby crafting and modeling, the significance of 3D printing emerges prominently. This innovative technology has transformed the way enthusiasts and professionals create miniatures, offering unparalleled precision and versatility. Understanding 3D printing for miniatures is not just about appreciating the end products; it’s about grasping the underlying processes that allow for fine detail, custom designs, and a degree of personal expression that traditional methods cannot match.
In the realm of tabletop games, for instance, the trend has swung towards customized figures and terrains crafted specifically for unique gaming experiences. With 3D printing, hobbyists can produce everything from intricate game pieces to full landscapes, elevating gameplay while leaving a personal mark. It's more than just a hobby; it often becomes a satisfying blend of art and technology.
Choosing the right 3D printer tailored for miniatures involves more than simply picking an affordable model. It warrants attention to several factors, including the printer's resolution, speed, and material compatibility. These elements heavily influence the quality of the printed miniatures and, subsequently, the satisfaction of the creator. A high-resolution printer can render intricate details that are vital for miniature figures, enabling smoother surfaces and more lifelike representations. However, it’s not just resolution that matters; a printer’s speed plays a critical role, too, especially when working on larger projects with multiple pieces.
Key Considerations
Here are some key points to consider when diving into 3D printing for miniatures:
- Technology Types: Different technologies yield varying results. Fused deposition modeling (FDM) might be more common in casual setups, while stereolithography (SLA) gives finer results but might be costlier.
- Learning Curve: Engaging with 3D printing means facing a learning curve. Various software and design programs come into play, requiring some understanding to ensure smooth operation.
- Community and Support: Joining 3D printing communities, such as those found on Reddit or Facebook, can be invaluable. Getting tips and sharing ideas with fellow enthusiasts can vastly improve your experience.
3D printing miniatures is not merely a phase; it’s part of a larger movement that champions creativity through technological innovation. Being informed about the machines and processes opens up endless possibilities for both personal and professional growth. In this article, we aim to navigate the nuances of selecting the best 3D printer for miniatures, ensuring that hobbyists and industry professionals alike can make the most informed choices possible. As we proceed, we'll delve into the intricacies of various printing technologies, key printer features, and much more.
"The future belongs to those who believe in the beauty of their dreams." — Eleanor Roosevelt
By understanding the fundamentals of 3D printing for miniatures, every creator can unlock the potential for making their designs a reality. Let’s embark on this journey together.
Understanding 3D Printing Technologies
When it comes to selecting a 3D printer for miniatures, grasping the various printing technologies is essential. Each method has its strengths and weaknesses, which can significantly impact the quality and efficiency of your prints. Understanding these technologies allows hobbyists and professionals alike to make informed choices that align with their specific needs and project goals. Knowing the ins and outs of these technologies can hone your skills, minimize challenges, and enhance your overall printing experience.
Fused Deposition Modeling
Fused Deposition Modeling, commonly referred to as FDM, is perhaps the most recognized and accessible form of 3D printing. This technique works by extruding thermoplastic filament through a heated nozzle, depositing layer upon layer to construct a 3D object.
The beauty of FDM lies in its versatility. It is suitable for a wide range of materials such as PLA, ABS, and PETG, making it an ideal choice for miniatures. Not to mention, the availability of filaments in various colors and textures adds another layer of personalization to your projects. However, while FDM printers are relatively affordable, the print resolution can vary. You might find that finer details in miniatures can sometimes suffer a bit as compared to other methods, which leads us to the next technology.
Stereolithography
Stereolithography (SLA) is a more advanced 3D printing method that utilizes a laser to cure liquid resin into solid plastic. The result is incredibly detailed prints, perfect for those intricate miniature designs. The layers produced by SLA tend to be much thinner than those of FDM, allowing for high precision and smooth finishes.
While SLA printers can be more expensive, their outputs often justify the cost, especially for professional-grade miniatures. Moreover, the range of resin materials available caters to different needs, from flexible to rigid options, enhancing the adaptability of this technology. On the flip side, SLA processes can be messy, and post-processing is often a necessary step, involving additional time and care.
Digital Light Processing
Digital Light Processing (DLP) operates similarly to SLA, yet employs a projector to flash an entire layer of the object at once, rather than scanning points with a laser. This can often result in faster print times, thus allowing you to churn out your favorite miniatures with less waiting around.
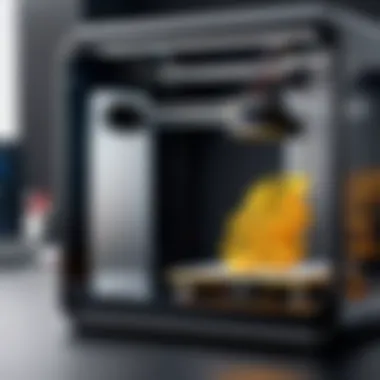
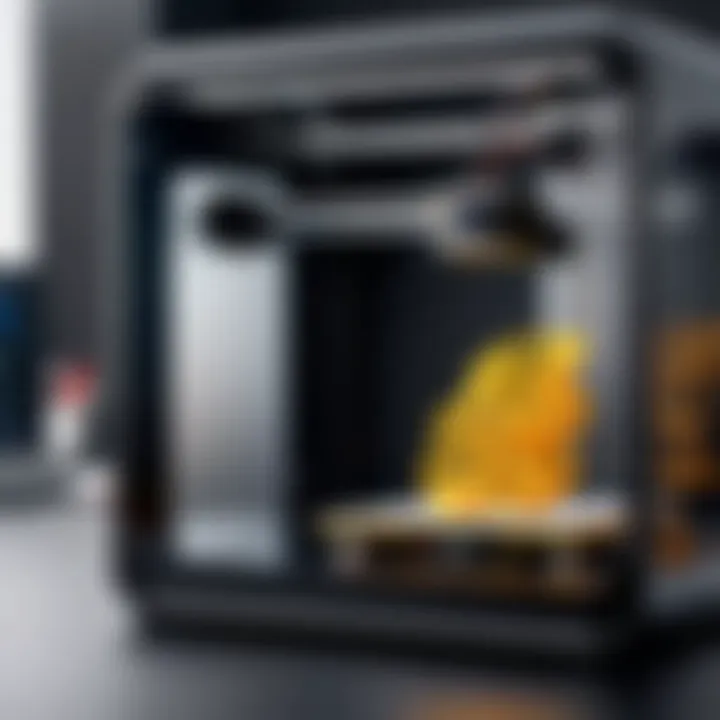
DLP printers also excel in producing fine details, rivaling those of SLA, but typically they have somewhat larger build envelopes, allowing for the printing of multiple miniatures at once. Just like SLA, the materials for DLP are resin-based, which means you'll need to consider the challenges related to curing and handling resins with this method. It’s also worth mentioning that the cost of DLP printers has been decreasing over time, making them a more appealing option for enthusiasts.
Understanding these 3D printing technologies will empower you to make choices that best suit your miniature printing endeavors. Each technology carries its unique characteristics that provide specific advantages and drawbacks, and knowing them will ultimately lead you to the printer that fits your needs like a glove.
Key Features to Consider
When it comes to choosing the right 3D printer for miniatures, it’s like hunting for the perfect spice to toss in your secret sauce. Certain aspects make all the difference in quality and overall user experience. Identifying key features enables hobbyists and professionals to match their specific needs to the right machine, resulting in superior prints and less frustration down the line. Here, we delve into the pivotal characteristics one should carefully ponder before pulling the trigger on a purchase.
Print Resolution and Detail
Print resolution is the bread and butter of 3D printing, especially for miniatures. Higher resolution means more detail—a must for replicating intricate designs and fine lines that capture the essence of your models. Resolution is measured in microns, with smaller numbers indicating finer details. A printer that offers a resolution of 50 microns, for example, can produce much sharper features than one limited to 200 microns.
- What to Check:
- Minimum layer height
- Maximum print size
- Nozzle diameter
Investing in a printer with exceptional print resolution can invariably elevate the quality of your miniatures, making them look professional and polished.
Build Volume
Size matters. A printer’s build volume dictates how large your prints can be. While a compact printer might suit someone working on small models, those looking to create larger figures or multiple pieces at once should pay close attention. A too-small build volume can send creativity tumbling down the rabbit hole of restriction.
- Considerations:
- Dimensions of your typical print
- Quantity of miniatures printed simultaneously
- Space available for the printer itself
A printer with a sufficient build volume can offer greater flexibility, allowing for larger works or more shapes churned out together.
Printing Speed
If you’re in a rush (and let’s be honest, who isn't sometimes?), printing speed is a notable factor. While you don’t want to sacrifice quality for speed, certain projects demand faster turnaround times. Different technologies assess speed on varied scales, measuring how many millimeters the print head moves per second.
- Look For:
- Average print time for different resolution settings
- User reviews on speed consistency
- The printer's handling of complex designs
Achieving a balance between quality and speed is no small feat, but it can drastically improve your workflow.
Material Compatibility
Next up is material compatibility—akin to checking the ingredients before baking a cake. Not all printers play nicely with the same filaments or resins. Some printers may only handle specific types, such as PLA, while others are more versatile, accepting various materials like PETG, ABS, or specialty resins.
- Essentials to Evaluate:
- Types of materials supported
- Availability of those materials in your region
- Any special requirements (temperature settings, etc.)
A printer that accommodates a broader array of materials increases flexibility and enables users to explore different textures, colors, and finishes.
User-Friendly Interface
A printer can boast the best hardware on the market, but if it’s as complicated as rocket science, even the most advanced users might struggle. A user-friendly interface—whether that’s a touchscreen, app integration, or simple navigating—can smoothen the learning curve. Ideally, you want it to be intuitive enough that even a newbie could get their feet wet without pulling their hair out.
- Key Features to Consider:
- Touchscreen vs. button interfaces
- Ease of accessing settings
- Compatibility with design software
Tools and features designed with the user in mind could lead to lower error rates and a more enjoyable printing experience.
Support and Community
Every great venture requires a solid support system. Whether it’s troubleshooting ink issues or finding the best slicing software, having a community or customer support can turn a challenging situation into a mere bump in the road. A vibrant community can also provide inspiration, sharing tips and tricks learned through experience.
- Why It Matters:
- Access to resources like user forums and tutorials
- Availability of technical support from the manufacturer
- Engagement with fellow users through platforms like Reddit or Facebook
Ultimately, a robust support ecosystem can enhance satisfaction and keep your miniatures flowing from the printer flawlessly.
Review of Leading Models
Choosing the right 3D printer for miniatures doesn't just hinge on the specifications and features of individual models. It's essential to consider the landscape of available options in the market. This section dives into a thorough review of leading models that cater specifically to the miniature crafting community. By evaluating different classifications—entry-level, mid-range, and professional-grade—hobbyists and industry professionals can pinpoint what fits their needs best.
The importance of this review lies in its practical implications. As you venture into the intricate world of miniature printing, various models may emit shine and allure but may not necessarily deliver on the specific requirements you have. It’s like choosing a dress for a formal occasion; just because it’s stylish doesn’t mean it’s suitable. Evaluating the leading models prepares one for an informed decision, focusing on intricacies such as usability, printing quality, and the overall experience with each machine.
Entry-Level Options
When embarking on the journey of 3D printing for miniatures, entry-level options often become the stepping stones for many enthusiasts. These models are typically budget-friendly and user-friendly, making them ideal for beginners wary of a high initial investment. Models like the Creality Ender 3 or the Anycubic i3 Mega have proven to be favorites amongst newcomers.
- Affordability: Entry-level printers usually cost less than $300, making them an enticing option for those just starting out.
- Ease of Use: Most of these printers come largely assembled or require minimal setup. Their simplicity often allows users to start printing within hours of unboxing.
- Community Support: As these models gain popularity, communities spring up around them on platforms like reddit.com and forums, providing helpful tips and tricks.
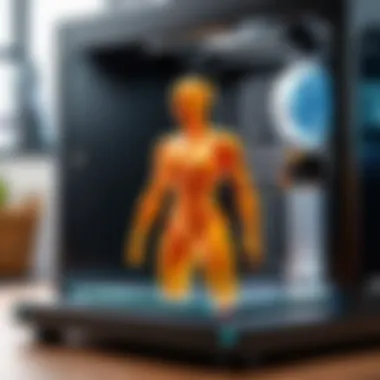
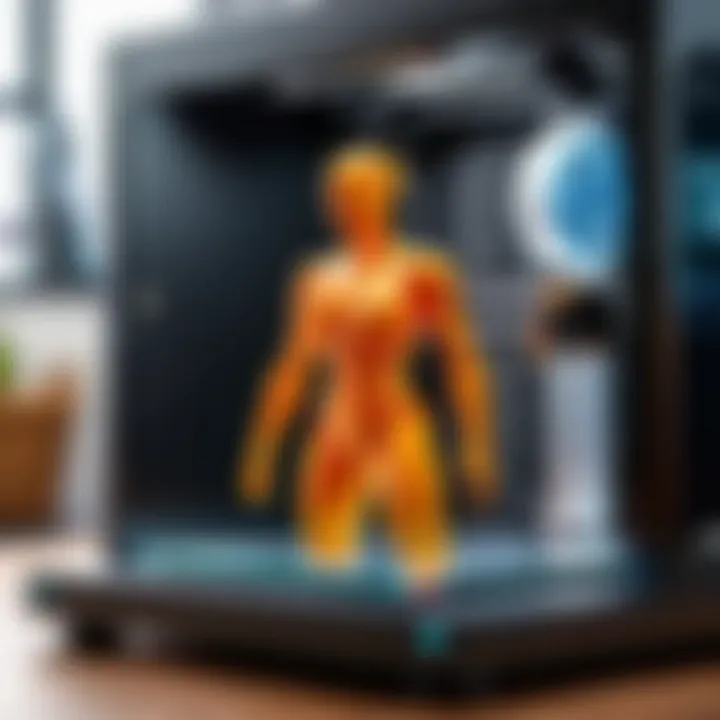
However, remember, entry models may limit aspects like printing speed and resolution, which might frustrate advanced users down the line.
Mid-Range Printers
Mid-range printers occupy a sweet spot for hobbyists looking to immerse themselves deeper into the craft without breaking the bank. Models such as the Prusa i3 MK3S or the Elegoo Mars 2 Pro strike a balance between cost and performance. Here, one can find features that cater to an advanced user base while still being accessible.
- Higher Print Quality: With better resolution capabilities, these printers deliver finer details for miniatures, essential for those who appreciate craftsmanship.
- Enhanced Build Volume: Many mid-range options offer a more generous build envelope compared to entry-level printers, enabling creators to handle larger designs or multiple pieces in one pass.
- Support for Diverse Materials: Often, mid-range printers can handle a broader range of filaments or resins, opening doors to multiple creativity outlets.
Investing in a mid-range printer might set you back between $400 to $1,000, but those willing to stretch their budget are likely to reap the benefits in the long run.
Professional-Grade 3D Printers
For those who are deep into the 3D printing game, professional-grade printers elevate the miniatures high above the understandings of average hobbyists. Models like the Formlabs Form 3 or the Raise3D Pro2 cater to seasoned creators and professionals.
- Unmatched Precision: These machines provide high-resolution capabilities and layer accuracy that can exceed expectations, ensuring every intricate detail is meticulously captured.
- Speed and Efficiency: Professional printers are designed for high-throughput production, making them excellent for businesses or serious hobbyists with large-scale projects.
- Comprehensive Features: With advanced software integration, many models support multiple materials and printing strategies, allowing users to push the limits of what’s possible in miniature design.
However, they come at a premium price ranging from $1,500 to well above $5,000, making them a substantial investment. Those who opt for these models should be ready for extensive knowledge and experience in the realm of 3D printing.
"Every model has its strengths and weaknesses, but careful consideration of your needs can reveal a printer that transforms your miniature vision into reality."
To summarize, the review of leading models equips enthusiasts and professionals alike with foundational insight into choosing the most suitable 3D printer for miniatures. It’s not just about what’s trendy or readily available; understanding the nuances and functionalities of each model can lead to a more enriching experience in the miniature printing domain.
Software Considerations
When it comes to 3D printing, the software is just as crucial as the hardware. Much like a conductor guiding an orchestra, slicing and design software orchestrates how your printer interprets and executes the intricacies of miniature designs. As a hobbyist or a professional, understanding the nuances of this software can significantly elevate your printing experience. It streamlines your workflow, enhances your designs, and ultimately impacts the quality of your printed miniatures. Let's break down the three core areas within software considerations that need attention.
Slicing Software
Slicing software is the bridge that transforms 3D models into a language your printer can understand – G-code. This software divides your model into thin horizontal layers, determining how each part should be printed, which is pivotal for achieving high resolution and detail. Consider this like preparing a lasagna; you need each layer strategically placed. Popular slicers such as Ultimaker Cura, PrusaSlicer, and Simplify3D offer different functionalities and features that can cater to both beginners and seasoned users.
Some benefits of effective slicing software include:
- Control Over Print Settings: You can adjust layer height, speed, and infill density, which can lead to better results.
- Support Structure Management: The software can automatically generate supports for overhangs, making complex prints feasible without sacrificing quality.
- Preview Functionality: Most slicers allow you to preview the print, which helps in identifying any potential flaws before the actual printing starts.
A specific example would be using PrusaSlicer to fine-tune your layer settings for a fine-detailed miniature. If you have a highly intricate model, tweaking the layer height from the standard 0.2 mm to 0.1 mm can make a dramatic difference in render quality.
Design Applications
While slicing software deals with taking a model and preparing it for printing, design applications help you create those models in the first place. Tools like Blender or TinkerCAD not only allow for the creation of original designs but also enable you to customize existing models. This is similar to being an artist—your canvas is the software, and the designs are your masterpieces.
Design software commonly provides:
- 3D Modeling Capabilities: Users can create or modify models using various shapes and tools.
- Integration with Slicing Software: Many design applications allow for direct export to compatible slicing software, saving time.
- Community Libraries: Platforms like Thingiverse and MyMiniFactory offer immense libraries where users can share their designs.
For instance, if you want to modify a dragon miniature, Blender can let you stretch the wings or alter the posture to fit your vision. This type of customization can set your work apart in the tabletop gaming community.
File Formats and Compatibility
Understanding file formats is essential in the world of 3D printing, as not all printers interpret files the same way. The most common format is STL, which most slicing software supports. However, there are others, like OBJ or AMF, that might offer additional features like color and texture data.
When selecting a printer, consider its compatibility with various file formats. This ensures you won't be pulled into a situation where the file you created cannot be processed. Moreover, here are some points to keep in mind:
- File Size and Complexity: Simpler files are generally more manageable, while complex models might require more powerful software and hardware.
- Format Conversion Solutions: Sometimes you may find yourself needing to convert files into another format. Software like Meshmixer or Autodesk can come in handy here.
- Printing Fidelity: Some formats retain more detail than others, which can be critical depending on your project's requirements.
"The right tools make the job easier, and in 3D printing, software is your most potent tool."
Engaging with the software landscape grants you an edge, ensuring your miniatures don’t just print, but shine.
Post-Processing Techniques
Post-processing might seem like an afterthought for some hobbyists, but it plays a crucial role in achieving the desired finish for your miniatures. After printing, it's not simply about taking a piece off the build plate and calling it good. The intricate details of any miniature often require additional care to truly shine. Post-processing techniques can elevate a basic print into a stunning display piece, and knowing these methods can save time and frustration down the line. Let's dive into some of the critical aspects of post-processing, starting with the basics of sanding and smoothing.
Sanding and Smoothing
One of the most fundamental post-processing techniques is sanding. It's particularly useful for removing the visible layer lines that are often left by the 3D printing process. Each printer has its quirks, and unfortunately, they can result in imperfections. These can turn out to be particularly noticeable on smaller miniatures where details matter.
- Benefits of Sanding:
- Improved Surface Quality: Sanding provides a smoother finish, which can help in subsequent painting or detailing. A scratchy surface simply won’t take paint well.
- Highlighting Details: Sometimes, the finest details can get lost in the texture of a print. A little sanding can uncover these features.
- Shape Refinement: In some cases, you may want to alter the shape slightly, making sanding an essential tool for your toolkit.
"A well-sanded surface prepares the canvas for color; leaving details visible and striking."
To get started, you should use sandpaper of various grits—generally, beginning with a coarser grit and gradually moving to finer ones. Around 200-grit to start, and then moving to 400-grit or 800-grit to finish is a commonly recommended approach. It's vital to be patient during this process; rushing can lead to inadvertently damaging the miniature.
Painting and Finishing
Once the miniature is properly sanded, it’s time to consider painting and finishing techniques. The step of adding color is not just about aesthetics; it serves to bring the miniature to life. The right paint can also work wonders in terms of adding depth to the model, allowing shadows and highlights to become more pronounced.
- Choosing Paints:
- Finishing Touches:
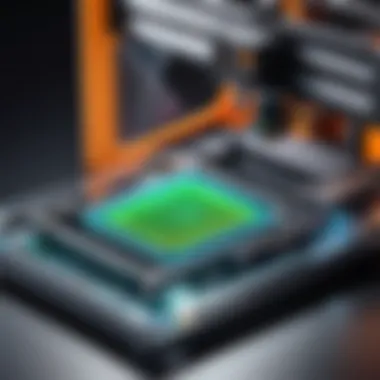
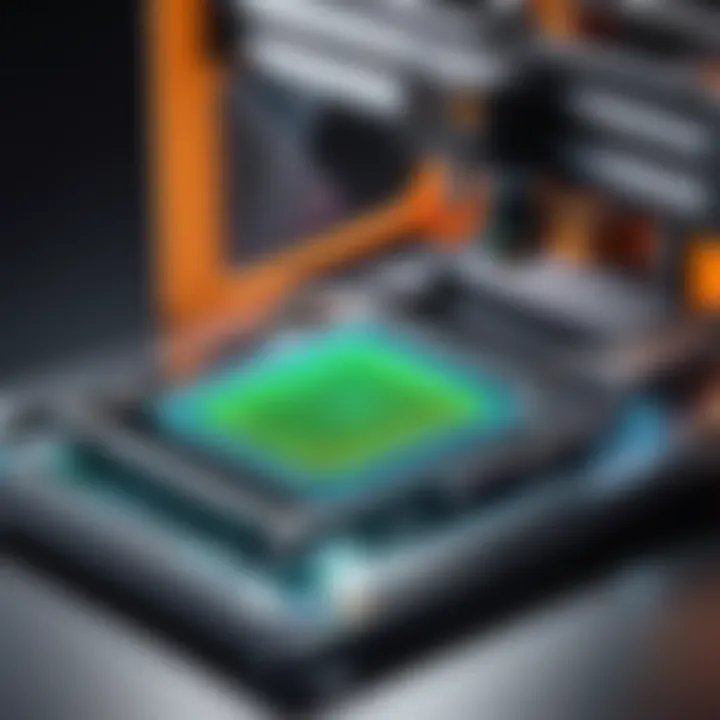
- Acrylics vs. Oils: Acrylic paints are favored for their quick drying time and ease of use for miniatures. However, oil-based paints can offer superior blending and texture effect but take longer to dry.
- Priming: Always start with a primer. This helps the paint adhere better and provides a uniform base color, which enhances the vibrancy of the final finish.
- Washes and Glazes: These can significantly enhance shadows and depth. Applying a wash can bring out the intricate details that might otherwise be lost.
- Sealing: After you have added all your layers of paint, a sealant is necessary. This can help protect your work, making it resilient to wear and tear.
By combining effective sanding and painting techniques, you can significantly impact the final presentation of your miniatures. This ensures each piece stands up to scrutiny for tabletop games, showcases, or just personal collections. Ultimately, mastering these post-processing skills can differentiate between a basic print and a work of art.
Cost Considerations
When diving into the realm of 3D printing for miniatures, understanding the costs involved is crucial. This isn't merely about the sticker price of the printer; it encompasses several layers that can significantly influence your overall investment. Analyzing cost considerations helps hobbyists and professionals alike to avoid potential pitfalls while maximizing their enjoyment and efficiency in 3D printing.
Initial Investment
The initial outlay for a 3D printer can vary widely depending on the technology and features you choose. For entry-level models, prices can start around a few hundred dollars, but for more advanced options, you might find yourself looking at thousands. It’s important to ask yourself: What am I truly looking to achieve?
Consider features like print resolution, materials compatible with the printer, and build volume—this helps in justifying the cost. For example, if you're aiming to create detailed miniatures with intricate designs, investing in a resin printer might be worth every cent, even if it feels like breaking the bank at first.
- Budget-Friendly Printers: Functionality often trumps price here, with machines that can produce satisfactory results without emptying your wallet.
- Professional Choices: These options may come equipped with advanced capabilities designed for intricate designs that can cater to more serious hobbyists or professionals.
Material Costs
Aside from the printer itself, another substantial factor to bear in mind is the ongoing cost of materials. Whether you opt for filament in FDM printers or resin in SLA printers, each bears its own price tags. Material costs can add up fast.
- Filament can range from $20 to upwards of $100 per kilogram, depending on quality and type.
- Resin tends to be pricier, often costing between $30 to $150 a liter.
This fluctuation necessitates planning, particularly if you're contemplating bulk orders for extensive projects. Furthermore, not all materials lend themselves to the same results, which means it may be worth experimenting until you find that sweet spot where quality meets affordability.
Maintenance and Upgrades
Long-term ownership involves considering maintenance costs and potential upgrades. 3D printers, much like cars or computers, require regular upkeep to deliver optimal performance. Some wear and tear is inevitable.
- Maintenance: Routine tasks such as cleaning the nozzle, recalibrating the printer, and replacing worn parts can incur costs, which, while not strictly prohibitive, should be accounted for in your budget.
- Upgrades: As technology evolves, you may find that newer components or kits enhance your printing capabilities—be it through improved print heads, better cooling systems, or upgraded slicing software. While upgrades can be tempting, they should be approached with caution.
As you journey through the world of 3D printing for miniatures, understanding these cost aspects will guide your decisions and facilitate an environment for learning and creativity. Planning your expenditures wisely can ultimately allow for more enjoyable projects, enhancing both your skills and your investment in this art form.
"In the end, the best printer for you is the one that meets your needs and your budget, balancing cost with the ability to create what you envision."
For additional insights and community discussions about the costs related to 3D printing, you can visit Reddit or explore detailed resources at Wikipedia.
Real-World Applications
In the rapidly evolving world of 3D printing, understanding its real-world applications is crucial, particularly when it comes to miniatures. The significance of this technology spans various fields and industries, making it not just a hobbyist's dream but a practical tool for professionals. For those choosing a 3D printer for miniatures, considerations extend beyond mere aesthetics and delve into functionality and efficiency.
Tabletop Gaming
One of the most vibrant markets for miniatures is tabletop gaming. Enthusiasts and casual players use these small models to enhance their gameplay experience in a plethora of games, from Dungeons & Dragons to Warhammer 40,000. Opting for a suitable 3D printer can lead to capturing intricate details and unique customization that mass-produced figures simply can't match.
With Fused Deposition Modeling or Stereolithography technologies, players can create characters or terrains that resonate with their unique narratives. Imagine having an army of hand-crafted warriors, each with its own backstory, designed on your living room table. This not only intensifies the engagement with the game but also fosters creative expression.
Moreover, there’s a strong community around tabletop games, providing robust support systems through group forums and social media. For example, many gamers share strategies for using specific printers designed for optimal output, be it for better layer detail or reducing print time. The community aspect makes it easier for new users to tackle challenges, allowing them to grow their skills while accessing support when needed.
Prototyping and Design
Beyond the realm of gaming, 3D printing has cemented its role in prototyping and design. Professionals in various sectors, such as engineering and product development, leverage this technology to create functional prototypes that can be rapidly tested and iterated. It’s a game changer — a real ace up one's sleeve.
With the right 3D printer, designers can generate realistic models of their products in a fraction of the time it would typically take using traditional methods. The flexibility in design allows for adjustments on-the-fly. Whether it’s creating complex geometric shapes or ensuring that parts fit together perfectly, the precision offered by modern 3D printers cannot be overstated.
Incorporating feedback quickly into designs is not just beneficial; it’s essential for meeting market demands efficiently. The ability to create a visual representation of a concept enables better discussions among teams and stakeholders. Still, not all printers are made equal. Certain models might excel at detail, while others could be better suited for larger prints. This means that your choice in a 3D printer can directly impact how well your design ideas come to life.
"A good prototype guides the designer and the manufacturer - it’s the bridge from idea to reality."
In summary, the real-world applications of 3D printing for miniatures extend far beyond simple hobbyist projects. Whether used in the realm of tabletop gaming or in the professional world for prototyping, understanding these applications is key to making informed decisions when selecting the optimal 3D printer. The blend of creativity and practicality ensures that both amateur and professional users can find substantial value in their investment.
End and Recommendations
In navigating the intricate world of 3D printing for miniatures, the conclusion of this article serves as a pivotal juncture for readers—be they hobbyists embarking on their miniature crafting journey or seasoned professionals refining their craft. The recommendations presented plunge into the essence of informed decision-making. These insights are not mere afterthoughts; they encapsulate the heart of an argument advocating for a discerning selection approach.
Importance of Informed Choices
Making an informed selection when choosing a 3D printer is not only about understanding the technicalities—print resolution, material compatibility, and speed—but also about aligning these features with one’s unique needs. A novice, for instance, might prioritize user-friendly interfaces over the intricate specifications sought by seasoned makers. As discussed throughout the article, the relevance of personal usage and goals cannot be overstated.
Key Considerations
When weighing your options, consider:
- Print Quality: Miniatures often demand precision; hence, prioritizing printers that excel in detail is crucial.
- Budget: Balancing initial investment with ongoing material and maintenance costs is key. Some printers might lure you with a low price tag but could prove costly over time with expensive materials or repair needs.
- Community Support: A vibrant online community can be a lifeline. Printer specific forums like those on Reddit or Facebook can be invaluable for troubleshooting and sharing tips.
Tailoring Recommendations
Based on analysis in previous sections, the recommendations for your printer choice could be categorized into:
- Beginners: Look for entry-level models that are forgiving to learn with and have a plethora of online resources. Brands like Creality and Anycubic often come highly recommended.
- Intermediates: If you have some experience under your belt, consider mid-range models that offer improved speed and reliability, such as the Prusa i3.
- Professionals: Those who work on detailed prototypes might lean towards high-end models like the Formlabs Form series, which specializes in fine detail and various resin types.
Final Thoughts
Ultimately, the journey to finding the optimal 3D printer for miniatures is unique to each individual. It's about understanding your needs, delving into specifics, and weighing the benefits against the costs. The right printer can elevate your miniature crafting experience to new heights—making it not just a task, but a joyful pursuit of creativity. Always keep in mind that the perfect fit for one may not necessarily be the same for another. Choosing the right printer equips you not just with a machine, but with the potential to bring your creative visions to life.