Exploring Large SLS Printers: Capabilities and Applications
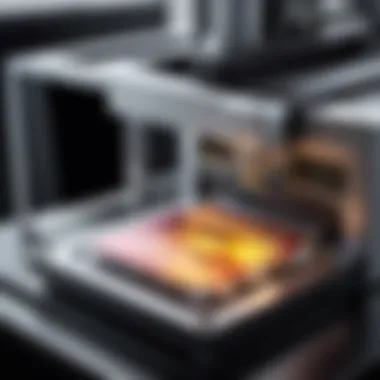
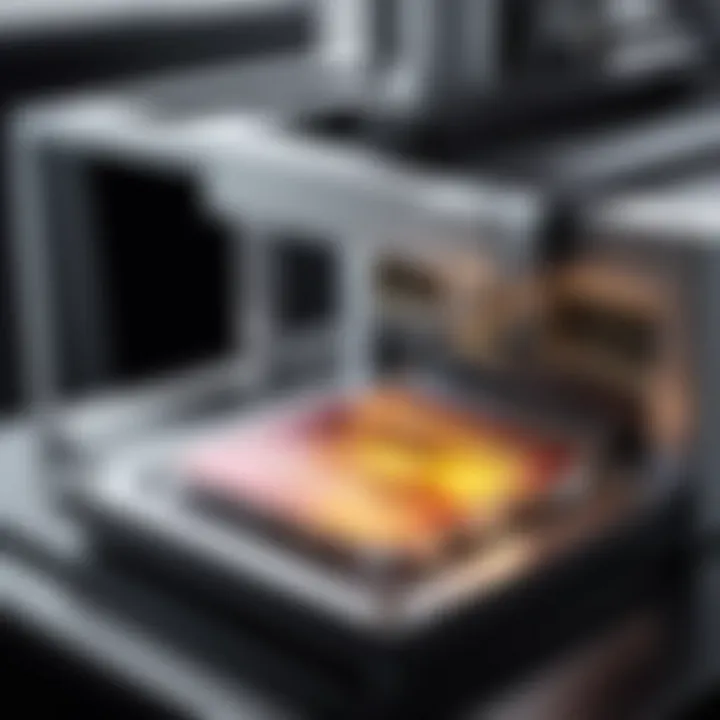
Intro
The realm of 3D printing has seen significant evolution, particularly with the advent of large Selective Laser Sintering printers. These machines are not merely another addition to the existing lineup of printing technologies; they represent a leap in terms of capabilities and applications. Large SLS printers are equipped to handle intricate designs while maintaining structural integrity and offering a variety of material options suitable for different industries, especially in the IT sector.
This article aims to provide a thorough examination of large SLS printers, focusing on key features, performance metrics, and practical applications. It will facilitate a better understanding for IT professionals looking to leverage this technology for competitive advantage. The overview will highlight important specifications, explore unique technologies, and consider future developments in additive manufacturing.
Overview of Product Features
Key Specifications
Large SLS printers boast a set of specifications that distinguishes them from their smaller counterparts and other 3D technologies:
- Build Volume: Many large SLS printers can produce parts with a significant build volume, allowing the creation of larger components without the need for assembly.
- Layer Resolution: Typically, these printers offer resolutions that range from 100 to 200 microns, ensuring high fidelity in detail reproduction.
- Heating Systems: Advanced thermal control mechanisms help maintain consistent temperatures throughout the build chamber, enhancing material properties and finishing quality.
Unique Technologies
Large SLS printers incorporate unique technologies that enhance their operational efficiency:
- Adaptive Laser Control: This technology allows for real-time adjustments in laser power and speed, ensuring optimal sintering and improving print quality.
- Material Recycling System: Many models come with integrated systems for recycling unused powder, making the process more economical and environmentally friendly.
- Multi-Laser Systems: Some high-end printers operate with multiple lasers, increasing production speed and efficiency, particularly for batch operations.
Design and Build Quality
Aesthetics
While functionality is paramount, the design of large SLS printers has also evolved. A modern large SLS printer is designed for efficiency, often taking into account factors such as:
- Ergonomic Interfaces: User-friendly interfaces simplify operation, reducing the learning curve for new users.
- Compact Footprint: Despite their size, many large SLS printers are engineered to maximize space efficiency in production environments.
Material Durability
The choice of materials significantly affects the durability of the resultant print:
- Material Selection: Large SLS printers support a wide range of thermal plastics like Nylon, TPU, and composites. Each material type offers unique properties suitable for different applications.
- Post-Processing Flexibility: Efficacy of post-processing techniques, such as surface treatments and sanding, allows for improved final product quality, enhancing both aesthetics and durability.
"Large SLS printers are not just about creating large objects; they focus on fine details that make a significant difference in practical applications."
Understanding SLS Technology
Selective Laser Sintering (SLS) represents a significant advancement in additive manufacturing, primarily due to its unique approach in creating three-dimensional objects. This section evaluates the foundational principles that govern SLS technology along with a comparative review against other 3D printing methods. Understanding these elements is crucial for IT professionals and tech enthusiasts who seek to leverage the distinct advantages offered by large SLS printers.
Foundational Principles of SLS
At the core of SLS technology lies the process of using a laser to fuse powdered materials layer by layer. Traditionally, the materials employed are thermoplastic polymers, but recent developments allow for a broader spectrum, including metals and ceramics. The laser selectively targets areas on a powdered surface, heating it to a point where sintering occurs, thus bonding the particles. This layer-by-layer construction results in highly intricate and complex geometries that are difficult to achieve with traditional manufacturing methods.
Key components of SLS technology include the laser system, powder handling system, and the temperature-controlled build chamber. Each component plays a pivotal role in determining the overall performance and quality of the finished products. Notably, SLS enables rapid prototyping, which is particularly invaluable in the fast-paced IT sector. By allowing faster production times and reducing material waste, SLS aligns with the lean manufacturing principles that many organizations adopt.
SLS vs. Other 3D Printing Techniques
Comparing SLS to other prominent 3D printing techniques, such as Fused Deposition Modeling (FDM) and Stereolithography (SLA) elucidates several advantages.
- Material Variety: SLS can work with a wide range of materials. In contrast, FDM mainly uses thermoplastics, and SLA primarily uses resins, which limits their applicability in certain sectors.
- Mechanical Properties: The parts produced through SLS generally exhibit superior mechanical properties. The sintering process ensures a stronger bond between particles compared to the layer adhesion seen in FDM.
- Design Freedom: Due to its ability to create complex geometries without the need for support structures, SLS enhances design flexibility, making it suitable for intricate designs often needed in technology applications.
However, SLS does have its limitations, such as higher initial setup costs and post-processing requirements. The operational demands and the expertise needed to manage these systems do require diligence but can yield significant returns down the road.
Understanding SLS technology is fundamental for professionals in the IT field. It highlights the operational efficiencies and design capabilities that can redefine production workflows. This foundation not only informs the eventual applications of SLS in the industry but also positions IT professionals to fully harness the potential of large SLS printers.
Design Features of Large SLS Printers
The design features of large SLS printers are crucial in defining their functionality, efficiency, and applications. Understanding these elements equips IT professionals and tech enthusiasts with the knowledge needed to leverage these machines effectively. Emphasis on design translates directly into operational advantages, ensuring that users achieve the highest output possible. By placing attention on key components, build volumes, and print accuracy, one can appreciate the practical implications of the technology.
Key Components
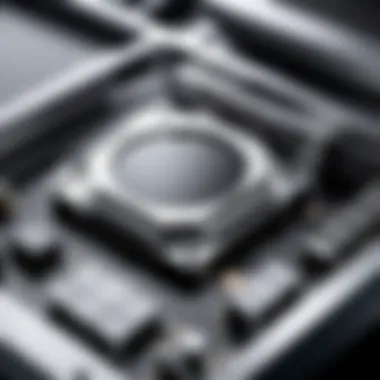
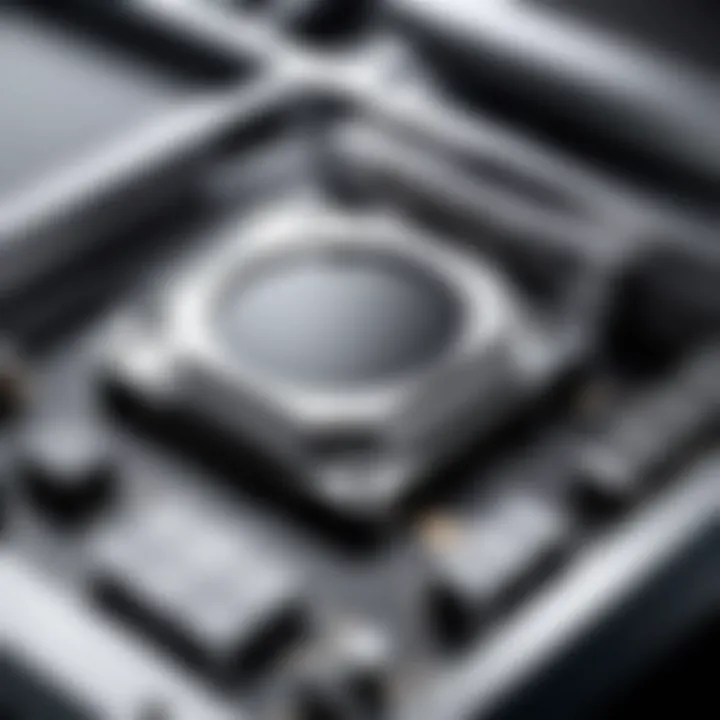
Large SLS printers comprise several key components that play a pivotal role in the overall printing process. Firstly, the laser system is fundamental. It uses high-powered lasers like CO2 laser to selectively sinter powder particles together. The precision of the laser resolves multiple factors including resolution and speed.
Secondly, the powder handling system is vital. This system manages the delivery and recycling of material during the printing processes. An efficient powder handling system minimizes waste and improves material utilization.
Additionally, the heating elements ensure that the powder is heated correctly while maintaining material properties. These elements play an important role in controlling the thermal environment during printing. Overall, understanding these key components leads to better operational performance of large SLS printers.
Build Volume Specifications
The build volume of an SLS printer defines the maximum dimensions of the objects that can be printed. This is an important consideration for industries requiring large prototypes or parts. Larger build volumes allow for greater productivity, as more parts can be produced in a single cycle. For instance, a machine with a build volume of 1000 x 1000 x 700 millimeters can create bigger and more complex geometries than smaller models.
Also, large build volumes often accommodate multiple part production in one go, which is cost-effective for businesses. Thus, the specifications of the build volume can directly influence project timelines and overall return on investment.
Enhancing Print Accuracy
Enhancing print accuracy in large SLS printers is essential for achieving high-quality outputs. Various techniques can be implemented to ensure precision. Calibration of the laser and regular maintenance of the printer are foundational steps. This includes ensuring the laser is optimally aligned and that the thermal conditions are stable.
Moreover, the use of advanced software facilitates pre-print analysis and adjustments. This software can simulate the printing process, allowing users to identify potential issues before they become problems in the actual print job.
Material Compatibility
Understanding material compatibility is crucial for large SLS printers. The effectiveness of the SLS process largely depends on the materials used. Compatibility affects not only the quality of the printed objects but also the overall efficiency of the manufacturing process. Therefore, comprehending different materials' properties allows IT professionals to select the best options for their specific needs, optimizing performance and reducing waste.
Common Materials Used
Large SLS printers are primarily known for their ability to work with various materials. The most common include:
- Nylon (Polyamide): This is perhaps the most widely used material in SLS printing. Nylon offers excellent strength and flexibility, making it suitable for functional prototypes and end-use parts.
- Thermoplastic Polyurethanes (TPU): TPU provides great elasticity, which is useful for parts requiring flexibility and durability, such as automotive components.
- Alumide: A mixture of nylon and aluminum powder, alumide has properties that enhance its strength and thermal stability while offering a unique finish.
- Glass-filled Nylon: This composite material enhances rigidity and thermal resistance, making it ideal for demanding applications.
These materials illustrate the versatility present in SLS printing. Their varied properties cater to diverse applications, giving professionals room to innovate.
Material Properties and Performance
Each material brings distinct characteristics that can influence the performance of SLS printed parts. For example:
- Mechanical properties: The tensile strength and flexibility of materials like nylon allow for the production of parts that can withstand stress and strain without breaking.
- Thermal properties: Some materials have high melting points, enabling them to endure hot environments, which is essential for aerospace and automotive industries.
- Surface finish: The quality of the material directly impacts the surface finish of the printed item. Smoother finishes are often desired for aesthetic reasons and functional performance.
Choosing the right material not only enhances performance but also impacts the lifecycle of the product.
Future Materials Trends
The future of materials for large SLS printers is evolving rapidly. Trends such as:
- Biodegradable Plastics: The push for sustainability drives interest in using eco-friendly materials that decompose over time, reducing environmental impact.
- Composite Materials: Increased use of reinforced composites is seen, improving strength while keeping weight low, which is crucial in aerospace applications.
- Multi-material Capabilities: Future SLS printers may increasingly incorporate the ability to handle multiple materials in one print job, enhancing customization and functionality.
These trends showcase the dynamic nature of material science in SLS printing, which continues to expand the possibilities for IT professionals and engineers alike.
Operating a Large SLS Printer
Understanding how to operate a large SLS printer effectively is essential for any IT professional or tech enthusiast engaged in additive manufacturing. Proper operation ensures not only optimal performance of the machine but also enhances the quality and reliability of the prints produced. Large SLS printers offer substantial advantages, including scalability and efficiency. However, these benefits can only be realized when the printer is set up, maintained, and operated with diligence.
Setting Up the Printer
To begin with, setting up a large SLS printer involves several critical steps. First, placement is crucial. Ensure that the printer is positioned in a controlled environment with sufficient ventilation and minimal dust. This helps to maintain the quality of the materials used and improves air circulation, essential for the printer’s laser system.
Next, you need to fill the powder bed with the right material. Materials in SLS printing often include nylon, polyamide, or other polymer mixtures. An appropriate amount of material must be added to prevent print failures. The powder must be evenly distributed to foster uniform thermal conditions across the build area.
Configuration of the software is another vital part of setup. Inputting correct parameters such as laser power, scanning speed, and layer thickness directly impacts print quality. Additionally, regular calibration of the laser is necessary for accurate performance across varying print jobs.
Maintenance Requirements
Regular maintenance is key to ensuring longevity and performance of large SLS printers. One must frequently check and clean both the laser optics and the powder handling system. Dust particles can accumulate, leading to ineffective laser functionality or poor print quality. Depending on usage, a detailed cleaning should occur at designated intervals, typically after every few print jobs.
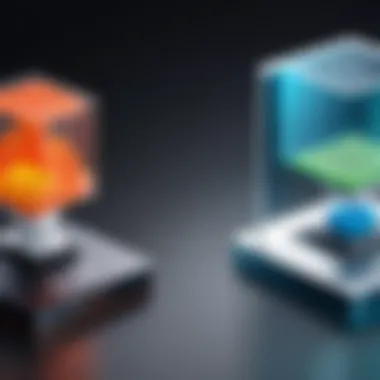
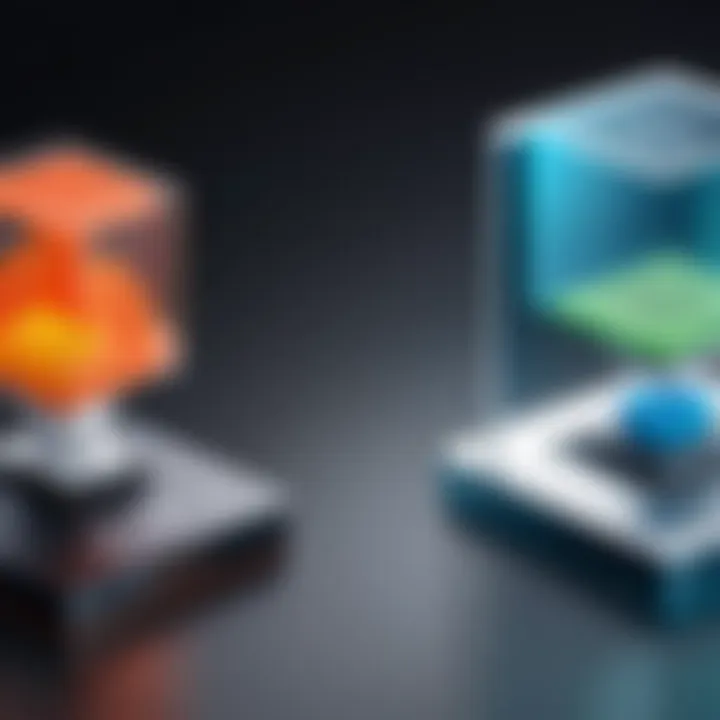
Moreover, monitoring the mechanical system for signs of wear is vital. Components such as the rollers and build platform should be inspected and replaced as necessary to avoid any disruptions during print cycles. Additionally, keeping an eye on the printer’s temperature regulations is prudent. High-performance SLS printers operate under specific thermal conditions, and any deviation can impact prints adversely.
Troubleshooting Common Issues
Even experienced operators can encounter issues with large SLS printers. One typical problem is warping or deformation of printed models. This is often due to differences in cooling rates among the printed layers. To mitigate this issue, adjusting the cooling rates and ensuring uniform temperature throughout the print can yield better results.
Another common issue is the failure to adhere to the build platform. This can occur for various reasons, including improper powder application or insufficient initial layer settings. It is beneficial to experiment with initial layer parameters to enhance platform adhesion.
Remember: Keeping logs of common problems and their solutions can save considerable time during future operations.
In summary, operating a large SLS printer encompasses meticulous setup, routine maintenance, and effective troubleshooting strategies. Professionals versed in these operational aspects can significantly improve production outcomes, ensuring the use of large SLS printers yields the desired results in the demanding IT landscape.
Performance Metrics in SLS Printing
Performance metrics in Selective Laser Sintering (SLS) printing provide critical insights into the operational excellence and effectiveness of this technology. Optimizing these metrics is essential for IT professionals and tech enthusiasts alike, who are looking to enhance productivity, quality, and innovation in manufacturing processes. By focusing on metrics like speed, surface finish, and dimensional accuracy, one can derive tangible benefits and make informed decisions about investments in large SLS systems.
Speed and Efficiency Evaluations
The speed of SLS printing is a primary concern for many industries. In general, faster print speeds lead to quicker project fulfillment, facilitating rapid prototyping and reducing time-to-market for products. Evaluating speed involves understanding not only the printing time but also the entire workflow, including pre-print and post-print processes.
A key aspect of improving speed is the selection of appropriate print parameters. For instance, using larger layer thicknesses can reduce print time but may impact the quality of the final part. Finding the right balance between speed and quality is essential.
Additionally, considering the efficiency of the printer during operation can lead to insights into energy consumption and material usage. Makers should also assess the technologies that enhance efficiency, such as multi-laser systems, which can significantly decrease overall printing times compared to single-laser configurations.
Surface Finish Considerations
Surface finish is another important performance metric that directly affects the usability of printed parts. In applications where aesthetics are crucial, such as in product design, achieving a high-quality surface finish is critical. The surface finish in SLS printing is affected by several factors, including the type of material used, layer thickness, and the laser's parameters.
Professionals should perform evaluations that may include:
- Roughness Measurement: Using tools like profilometers to assess surface roughness can help in understanding the finish quality.
- Post-Processing Techniques: Evaluating various post-processing methods, such as sanding, polishing, or coating, can enhance surface finish further.
An effective approach to control the surface quality is to closely analyze the molecular behavior of the materials during the sintering process. By optimizing the sintering temperature and time, the bond formed between powder particles can yield smoother surfaces.
Dimensional Accuracy Standards
Dimensional accuracy is vital in sectors that require precise part dimensions. This metric assesses how closely the dimensions of the printed part match those specified in the design file. High dimensional accuracy ensures that parts fit together correctly, which is essential in assemblies and functional components.
To measure and maintain accuracy, several standards and practices can be followed:
- Calibration: Regular calibration of the printer helps maintain output precision.
- Temperature Control: Ensuring that the build environment is kept at optimal temperatures reduces warping and other dimensional issues.
Companies often utilize Coordinate Measuring Machines (CMM) or laser scanners to perform inspections on printed parts. Acceptance criteria should be established based on application requirements to determine whether the accuracy meets the necessary standards.
"In the realm of large SLS printing, understanding performance metrics is as essential as the technology itself. It allows for streamlined operations and enabling innovations that drive success in a competitive landscape."
By diligent evaluation of these performance metrics, IT professionals can enhance their decision-making processes, leading to improved strategies for implementing SLS technology in various applications.
Applications in the IT Field
Large SLS printers stand at the intersection of innovation and practicality, particularly within the Information Technology sector. Their capabilities to create complex geometries and functional components enable organizations to shorten the development cycles significantly. In an industry where speed, precision, and customization are paramount, understanding these applications becomes essential for IT professionals aiming to leverage the full potential of additive manufacturing.
Rapid Prototyping
Rapid prototyping is one of the most impactful applications of large SLS printers. In a fast-paced IT landscape, the ability to quickly prototype designs greatly eases the iterative process of product development.
- Cost-Effective Testing: Unlike traditional methods, SLS allows for rapid iteration without substantial capital investment. This is crucial for testing software case designs or hardware enclosures across various specifications.
- Complexity in Design: SLS printers enable the creation of complicated geometries that might be impossible to achieve with subtractive manufacturing methods. This offers flexibility for designers to explore new ideas without immediate concerns over manufacturability.
- Speed of Production: The speed at which SLS can produce prototypes enhances the overall workflow for software and hardware integrations in IT projects. Being able to physically assess a prototype before full-scale production saves both time and resources.
Custom Tooling Solutions
Custom tooling is vital in manufacturing and assembly processes, particularly in the IT field where unique components are often required. Large SLS printers offer substantial benefits in creating tailored tooling solutions.
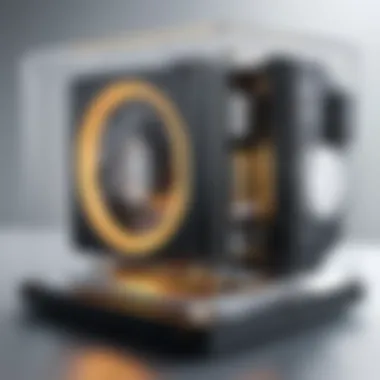
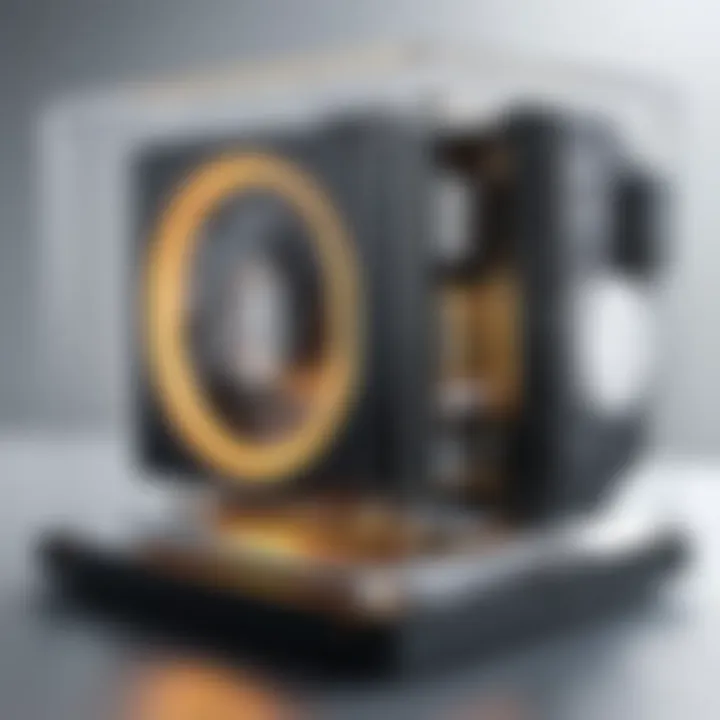
- Tailored Fit: Companies often face challenges with standard tools that do not meet specific requirements. Custom fixtures and jigs produced via SLS improve accuracy and efficiency.
- Short Lead Times: By eliminating the need for extensive tooling setup, SLS reduces lead times significantly. This responsiveness to project demands keeps technology initiatives on schedule.
- Material Optimization: Different industries require tooling solutions with varied material properties. SLS allows for a range of thermoplastic materials to be used, providing the necessary strength and durability for tooling purposes.
End-User Product Development
The end-user development within IT often entails designing components that meet specific user needs. Large SLS printers facilitate this critical process through various mechanisms:
- Customization Options: The ability to customize end-user products ensures that solutions cater to specific requirements. For example, custom cases for devices can incorporate unique branding elements or functional features.
- User Testing: Producing end-user products for testing can occur rapidly, providing users with real-world feedback before mass production. This can lead to a better quality product that aligns with user expectations.
- Sustainability: Using SLS for end-user product development can also lead to reduced waste compared to traditional methods. This contributes positively to sustainability goals within organizations.
In summary, the applications of large SLS printers in the IT field are vast and varied. From rapid prototyping that accelerates development cycles to customized tooling solutions that enhance manufacturing efficiency, their potential to transform operations cannot be overstated. Understanding these applications is vital for IT professionals.
Cost Considerations
Cost considerations are paramount in the decision-making process surrounding the adoption of large SLS printers. For IT professionals and tech enthusiasts, understanding all elements tied to costs can facilitate informed investments. The upfront costs, ongoing operational expenses, and return on investment metrics capture essential facets of the financial landscape related to SLS technology.
Initial Investment Analysis
When acquiring a large SLS printer, initial investments can vary significantly based on the model and its specifications. High-end printers often come with advanced features, such as enhanced build volumes and multiple laser options. It is crucial for professionals to conduct a thorough analysis of what each potential system offers against its price.
- Price Range: Depending on the manufacturer, prices of large SLS printers can range from tens of thousands to several hundred thousand dollars.
- Features Evaluation: Buyers should assess features like print speed, material versatility, and post-processing capabilities.
- Funding and Financing Options: Many vendors provide financing options that can ease the burden of upfront costs.
Ultimately, evaluating initial investments involves more than just the purchasing price—it also means considering the potential for scalability and integration within existing workflows.
Operational Costs Overview
Understanding operational costs is vital for maintaining budgetary discipline once an SLS printer is operational. Here, a few key elements come into play:
- Material Costs: The choice of materials can vary widely. Some polymers might be economical, while specialty materials can inflate costs significantly.
- Energy Consumption: Large SLS printers typically require considerable energy, impacting overall operating costs. Monitoring energy consumption can help manage expenses.
- Labor Expenses: Qualified personnel are essential for optimal printer operation. Training costs and salaries should be factored in as regular operational expenditures.
In summary, operational costs are ongoing and can influence the overall cost-effectiveness of using large SLS technology.
Return on Investment Metrics
Measuring return on investment (ROI) for large SLS printers is essential for justifying the initial outlay and ongoing costs. IT professionals should consider various metrics:
- Productivity Gains: Evaluate the speed and efficiency improvements against traditional manufacturing processes. Higher throughput can lead to substantial savings over time.
- Cost Savings: Analyze how SLS can reduce material waste compared to other manufacturing methods. Less waste means lower material expenses.
- Market Advantage: The ability to produce rapid prototypes and custom parts can place businesses ahead of competitors. This aspect of ROI is often qualitative but is critical to assess.
Overall, calculating ROI requires a comprehensive look at both tangible and intangible benefits resulting from the use of large SLS printing technology.
Future Trends in Large SLS Printing
The landscape of large SLS printing is continuously evolving, driven by technological innovation and growing market demands. Understanding future trends is crucial for IT professionals and tech enthusiasts, as these developments influence not only the capabilities of large SLS printers but also their applications and overall industry direction. By examining technological advancements, market forecasts, and potential new applications, professionals can prepare for and strategically position themselves in this dynamic field.
Technological Advancements
Technological progression remains a cornerstone of the future for large SLS printers. Key areas where advancements are occurring include:
- Improved Materials: Enhanced polymer materials, including composites that offer superior mechanical properties and thermal resistance, are under development. These materials enhance the durability and functionality of printed components.
- Automation Integration: Increasing automation in the printing process is reducing labor costs and minimizing human error. This includes advancements such as automatic powder handling systems and enhanced software for better print management.
- Monitoring Systems: Implementation of advanced sensors and AI for real-time monitoring during printing is gaining traction. These systems can provide valuable data about the printing process, allowing for quick adjustments and improved outcomes.
Such advancements not only elevate the performance of large SLS printers but also expand their potential use cases. As technology continues to mature, organizations must stay informed and adapt to leverage these tools effectively.
Market Forecast Analysis
Analyzing market trends helps stakeholders make informed decisions regarding investments and strategic planning. The SLS printing market is expected to experience significant growth due to several factors:
- Increased Adoption: More industries, including aerospace and automotive, are adopting SLS printing for rapid prototyping and production. This trend is likely to persist and expand across various sectors.
- Cost Reduction: With continuous advancements, the cost of operating large SLS printers is expected to decrease. As materials and technologies become more affordable, small and medium enterprises may also enter the market, increasing competition and driving innovation.
- Global Marketplace Expansion: The SLS market is not limited to a specific region. As businesses recognize the benefits, markets in Asia, Europe, and North America will see further expansion.
Such market dynamics indicate a promising future for businesses involved in large SLS printing. Forecasting, based on current trends, can inform investments, product development, and potential market entry strategies.
Potential New Applications
The versatility of large SLS printers opens doors to various innovative applications. Future directions may include:
- Healthcare Innovations: Custom implants and medical devices with tailored geometries designed through SLS technology may revolutionize healthcare. Personalized solutions are increasingly being recognized for their potential.
- Sustainable Manufacturing: Techniques that leverage recycling used materials into new products are becoming more prevalent. Sustainability goals will likely influence manufacturing processes, making large SLS printing a key player in eco-friendly production.
- Architectural Prototyping: Large SLS printers could reshape architecture by enabling the creation of complex prototypes rapidly, offering architects new ways to visualize their designs.
The expanding applicability of large SLS printing illustrates not just the technology's adaptability but also its potential to impact various industries significantly. Marketers and developers should stay ahead of these trends to capitalize on new opportunities.
"Understanding the future of large SLS printing is not merely an academic exercise. It's essential for anyone looking to leverage its technology effectively to meet upcoming demands in diverse markets."